The advent of 3D laser vibrometry has revolutionized the way industries monitor and analyze vibrational phenomena. This cutting-edge technology offers unparalleled precision, enabling experts to efficiently diagnose and solve engineering challenges. As an advanced, non-contact measurement tool, the 3D laser vibrometer stands out for its versatility, proving invaluable across various fields such as automotive engineering, aerospace, and industrial manufacturing. Offering real-time data acquisition, this device empowers engineers and researchers with the actionable insights they need to enhance product quality and machinery reliability.
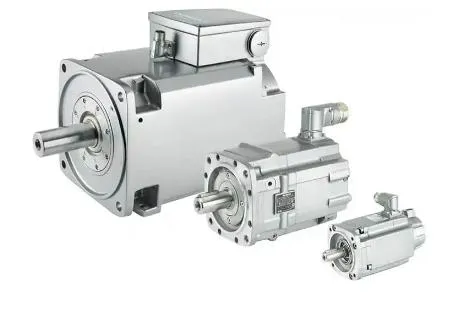
Key to understanding the significance of 3D laser vibrometers is their capacity to capture vibrational data with incredible accuracy. Unlike traditional contact-based measurement tools, laser vibrometers can scan and analyze an object's surface without physically interacting with it. This non-intrusive method preserves the integrity of the test object, eliminates mass loading effects, and ensures a more authentic representation of the vibrational characteristics. Consequently, industries can perform detailed modal analysis and dynamic testing without the constraints posed by physical sensors.
In practice, a 3D laser vibrometer employs laser beams to measure the velocity and displacement of an object's surface in three dimensions. The integration of digital signal processing allows for the simultaneous assessment of numerous measurement points, thereby providing comprehensive spatial data. This capability facilitates an exhaustive analysis of complex structures, enabling engineers to predict potential failure points and optimize designs accordingly. Moreover, the precision obtained through 3D laser vibrometry supports compliance with stringent safety and performance standards, inherent to sectors that demand high reliability.
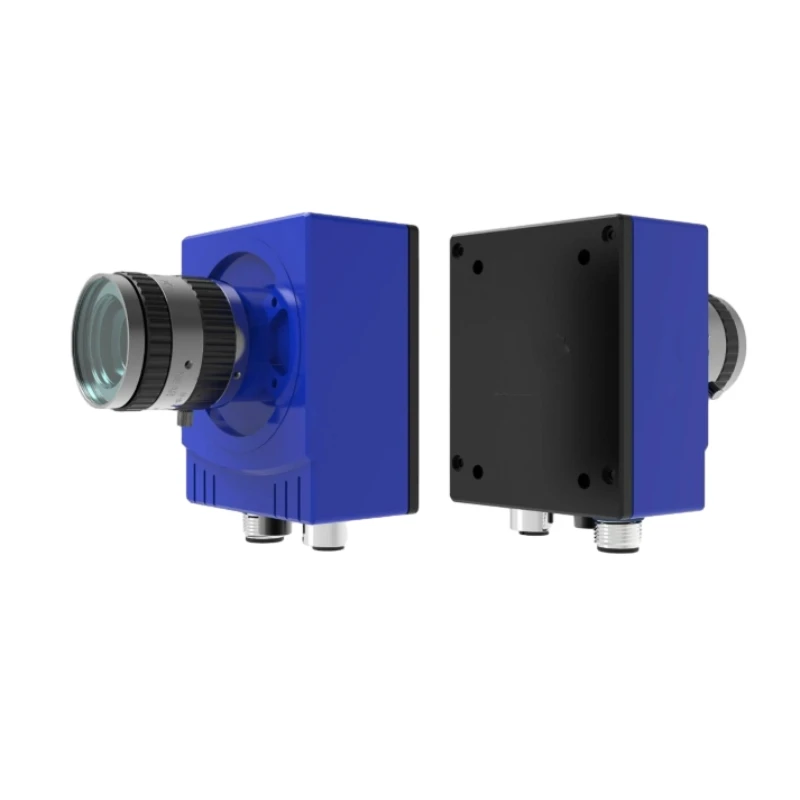
In the automotive industry,
the application of 3D laser vibrometers is transformative. Engineers employ this technology to investigate noise, vibration, and harshness (NVH) concerns, which are critical to enhancing vehicle comfort and functionality. It allows for a meticulous evaluation of powertrain components, suspension systems, and body structures. By identifying sources of undesirable noise or vibration, automotive manufacturers can refine their designs to mitigate these effects, ultimately delivering a superior driving experience. Additionally, the capability to rapidly acquire data fosters a more agile development cycle, crucial in a fiercely competitive market.
3d laser vibrometer
Equally impactful is the role of 3D laser vibrometry in aerospace engineering, where precision and reliability are paramount. Vibrational analysis of aircraft components such as turbines, wings, and fuselages is essential to ensure structural integrity and performance. Given the complexities of aerospace systems, 3D laser vibrometers provide the necessary spatial resolution to capture nuanced vibrational patterns. This allows engineers to perform detailed fatigue analysis and conduct rigorous fault diagnosis, thereby ensuring that aircraft not only meet design specifications but also maintain operational safety throughout their service life.
Beyond these sectors, 3D laser vibrometers are instrumental in industrial manufacturing for machine condition monitoring and predictive maintenance. By continuously analyzing vibration patterns, this technology enables the early detection of issues such as misalignments, imbalances, or bearing faults. Consequently, maintenance activities can be scheduled proactively, minimizing downtime and extending machinery lifespan. This proactive maintenance strategy reduces operational costs and enhances production efficiency, reinforcing the critical role of 3D laser vibrometers in modern manufacturing systems.
Integrating 3D laser vibrometry into routine operations necessitates understanding and expertise. Companies must invest in training personnel to interpret data accurately and make informed decisions. Collaborating with experienced vendors ensures access to the latest advancements in vibrometry technology and best practices, thus maximizing the return on investment.
As industries become increasingly aware of the benefits of 3D laser vibrometry, the demand for this technology continues to surge. Its application not only facilitates precision engineering but also underpins a culture of continuous improvement and innovation. For businesses poised to remain at the forefront of their sectors, adopting 3D laser vibrometry is not just an option but a necessity. The future of industrial diagnostics and analysis is here, promised by the unparalleled capabilities of 3D laser vibrometry.