The realm of dimensional inspection has drastically evolved, bridging the gap between traditional methods and cutting-edge technology. Among the forefront of these innovations lies laser scanning, a pivotal advancement in ensuring precision and quality in manufacturing processes. This article delves into the dynamic advantages of laser scanning dimensional inspection from both an experiential and expert standpoint, reinforcing its standing as a reliable and authoritative solution in the industry.
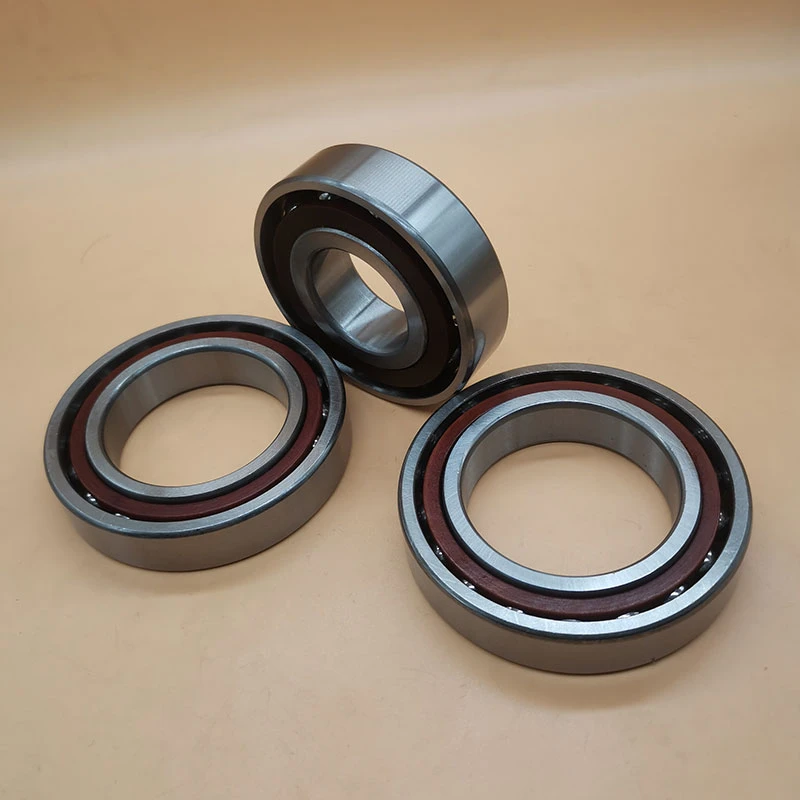
Experience Every layer of expertise in manufacturing acknowledges the critical importance of precision. Earlier, companies relied on manual measurements which were not only time-consuming but also susceptible to human errors.
The transition to laser scanning has been revolutionary. Companies now experience unprecedented efficiency; complex geometries that once required arduous manual inspection are now effortlessly captured with laser scanning technology.
Employees recount the first time they used laser scanners; there was a significant reduction in inspection cycles and scrap rates. This enhancement is not merely theoretical but a tangible experience that has seen widespread acknowledgment across various sectors, from automotive to aerospace.
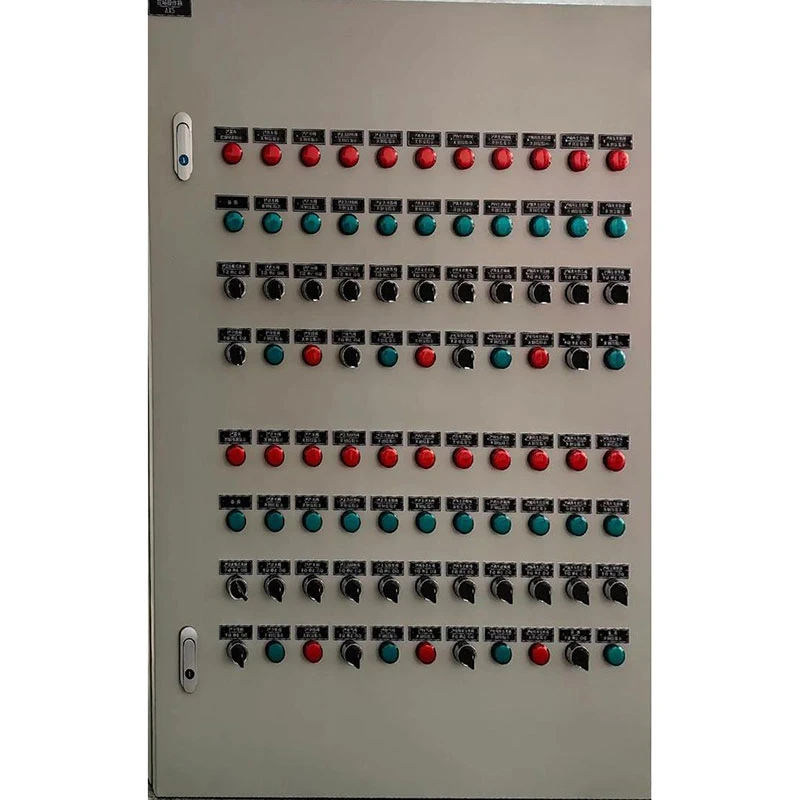
Expertise Laser scanning operates on a principle of projecting a laser beam over the object to be measured. The reflected light is then captured by sensors which create an accurate 3D model. This method surpasses traditional contact-based measurement due to its non-destructive nature and adaptability to scan complex, irregular shapes.
Professionals in the field emphasize its capability to capture millions of data points in seconds, providing a comprehensive surface profile that is paramount in quality control. The expertise of using laser scanners transcends simple usage; it involves understanding data analysis, software integration, and precise calibration to harmonize scan data with pre-determined CAD models.
Laser scanning size inspection
Authoritativeness Industry leaders and authoritative bodies have acknowledged the superiority of laser scanning in improving manufacturing standards. This endorsement underscores the technology's critical role in contemporary quality assurance paradigms.
Standards organizations, including ISO, have incorporated guidelines for laser scanning, recognizing its impact in upholding stringent quality benchmarks. Manufacturers who adopt laser scanning are often seen as pioneers, leading industry standards by integrating best practices in their processes.
Trustworthiness The reliable nature of laser scanning dimensional inspection builds a solid foundation of trust with clients and stakeholders. Businesses that leverage this technology assure their clientele of a commitment to delivering high-precision products consistently.
Case studies reveal that clients experience fewer post-production modifications and failures due to the reliability of laser-verified measurements. The scanner's ability to document and archive each inspection further boosts trust, providing traceability and accountability rarely matched by other methods.
In conclusion, the integration of laser scanning into dimensional inspection is not a mere technological upgrade but a transformational shift that addresses the very core of manufacturing challenges. Through enhanced precision and efficiency, rigorous industry endorsement, and unwavering reliability, laser scanning stands as the epitome of modern inspection solutions. It’s a testament to how embracing innovative technology can elevate quality standards, paving the way for future-forward manufacturing practices.