Integrating laser scanners with Coordinate Measuring Machines (CMMs) is reshaping the landscape of precision measurement in manufacturing and quality control. This combination marries the meticulous accuracy of CMMs with the rapid data collection capabilities of laser scanners, offering an unmatched solution for industries demanding high precision and efficiency.
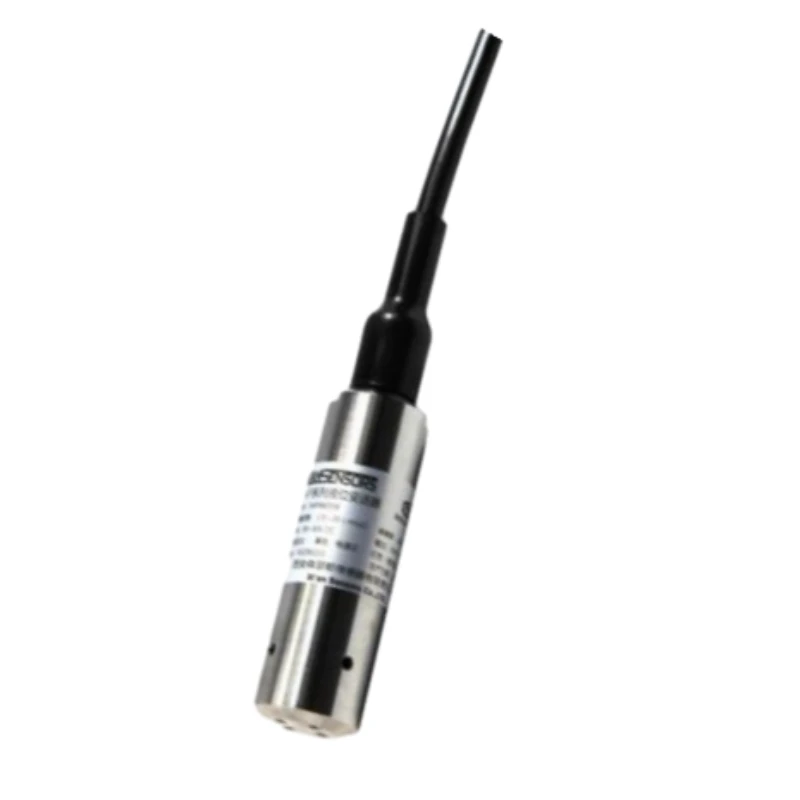
Laser scanners attached to CMMs bring a new level of sophistication to dimensional analysis. While traditional tactile CMM probes offer high accuracy, they can be time-consuming, especially when dealing with complex geometries. Laser scanners overcome this limitation by rapidly capturing millions of data points across an object's surface. This ability to quickly amass comprehensive surface data streamlines the inspection process, significantly reducing cycle times without compromising accuracy.
A major advantage of laser scanner-equipped CMMs lies in their non-contact measurement approach. This is especially valuable when dealing with delicate or flexible materials that could be deformed or damaged by touch probes. Laser scanning is ideal for measuring soft materials like rubber or thin plastic parts where deformation must be avoided to ensure that the measurements reflect the part's true geometry.
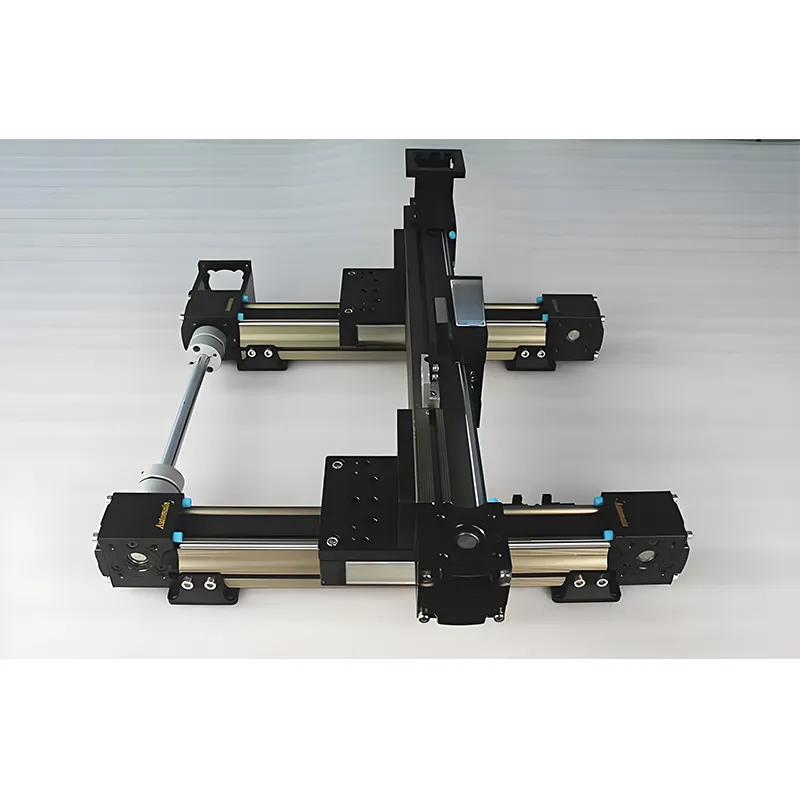
Expertise in implementing laser scanners with CMMs also enhances reverse engineering processes. When detailed CAD models are unavailable, scanning an existing part can create an accurate digital representation, aiding in the development or modification of components. This capability is invaluable in sectors such as aerospace and automotive, where it can be used to recreate legacy parts or facilitate rapid prototyping within the design phase.
Furthermore, the expertise required to effectively deploy and operate laser scanners with CMMs extends to software proficiency. State-of-the-art software solutions integrate seamlessly with hardware to provide user-friendly interfaces and powerful analysis tools. These software platforms play a crucial role in processing the vast datasets collected by laser scanners, converting raw point clouds into actionable insights on part conformity and deviation from specification.
cmm with laser browser
As industry standards and customer demands continue to evolve, the adoption of laser scanners integrated with CMMs stands as a testament to innovation in metrology. With the ongoing advancements in scanning technology, such combinations are only set to improve, promising faster data acquisition times, greater accuracy, and deeper insights into complex geometrical structures.
Trustworthiness in using laser scanner-equipped CMMs stems from the accumulation of real-world application data and case studies highlighting successful implementations across industries. Success stories from automotive manufacturing lines, for instance, underscore the robust accuracy and efficiency gains in quality control and inspection protocols when utilizing such hybrid systems.
In an era prioritizing precision and speed, organizations leveraging laser scanner-CMM integrations position themselves at the forefront of manufacturing excellence. By investing in such technology, companies not only enhance their inspection capabilities but also cement their reputation for quality—delivering products that meet the most rigorous specifications while optimizing operational workflows.
With a keen focus on maintaining authoritativeness, experts recommend regular calibration and certification of both laser scanners and CMMs, ensuring that measurement systems operate within specified tolerances. Ongoing training for staff handling these sophisticated instruments is equally crucial, cultivating a skilled workforce equipped to harness the full potential of this technology.
In conclusion, the convergence of laser scanners with CMMs represents a paradigm shift in precision measurement, blending speed, accuracy, and flexibility. It addresses modern industry challenges and keeps pace with the push towards advanced manufacturing practices, making it an indispensable asset for companies striving for competitive advantage and excellence in quality standards.