Embracing the future of manufacturing and prototyping, the laser 3D printing technology, known as lazer ile 3d in Turkish, stands as a remarkable innovation that is rapidly transforming industries across the globe. With an increasing demand for precision, speed, and cost-efficiency, businesses are turning towards laser 3D printing as a solution that meets and exceeds these expectations.

Laser 3D printing’s profound impact is particularly evident in the aerospace industry, where the need for light yet robust components is paramount. The technology employs a concentrated laser to fuse powdered materials, layer by layer, creating intricate geometries that were previously unattainable. By allowing the production of complex structures that provide aerodynamic efficiency while reducing fuel consumption, laser 3D printing plays a pivotal role in modern aviation engineering. Manufacturer studies confirm that certain aircraft components made using this method result in a weight reduction of up to 60%, contributing to significant cost savings and efficiency enhancements.
Moving beyond aerospace, the medical sector is another arena where laser 3D printing demonstrates its versatile potential. It enables the production of patient-specific implants and prosthetics with a level of customization impossible through traditional manufacturing methods. Surgeons and medical engineers can now create parts that mirror the intricate architecture of human tissues, vastly improving patient outcomes. Clinical trials report that bone implants crafted using laser 3D printing not only fit precisely but also promote faster integration with native bone structures, showcasing the technology’s promise for future medical advancements.
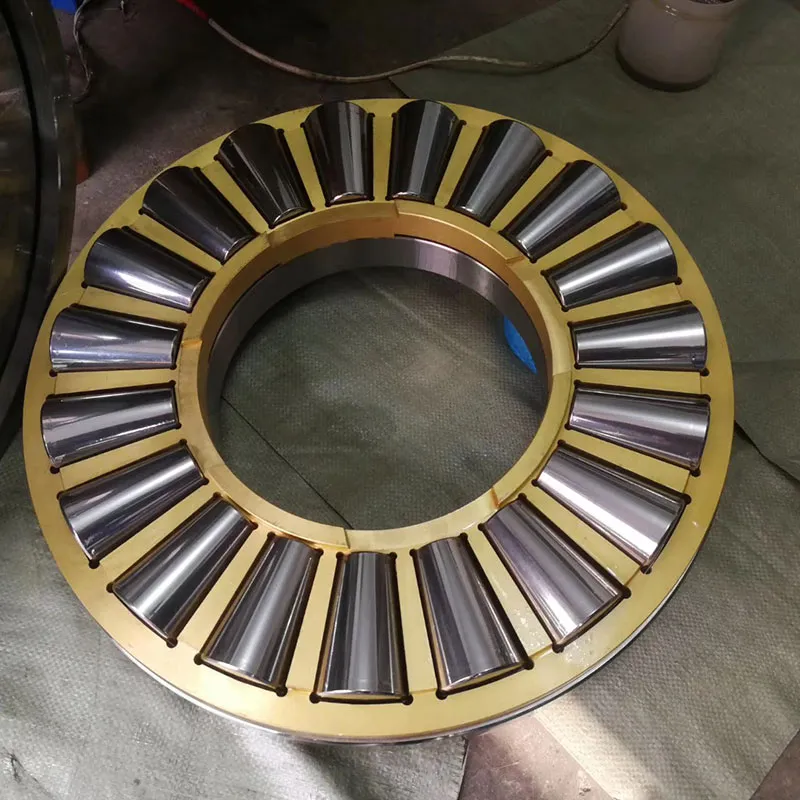
In automotive manufacturing, laser 3D technology offers a revolution in prototyping and production. By significantly shortening the product development cycle, companies can achieve faster time-to-market for new vehicle models.
The ability to swiftly iterate designs without the delay of conventional prototyping methods provides a competitive edge. Automakers utilizing this technology report an acceleration of their design processes by up to 30%, which allows them to respond rapidly to market trends and consumer demands.
3d with lazer
The energy sector also benefits from laser 3D printing, particularly in the development of efficient and compact components for renewable energy solutions. The production of wind turbine parts, for example, can be optimized for strength and minimal material usage, thanks to the unique capabilities of laser-based additive manufacturing. As renewable energy targets climb globally, industries are recognizing the technology's potential to produce components that not only meet but set new standards for performance and sustainability.
Despite these remarkable applications, implementing laser 3D printing requires deep expertise and understanding of materials science and laser technology. Businesses venturing into this area must ensure they collaborate with knowledgeable experts and establish robust quality assurance processes. The precision and high energy involved in laser 3D processes demand strict adherence to safety protocols and regulatory compliance, which can be a hurdle without proper guidance. Continuous training and research are vital to maintaining the highest standards of production and product integrity.
Finally, trustworthiness in this innovative field is built through demonstrated success and adherence to industry standards. Companies utilizing laser 3D printing must be transparent about their processes and collaborate closely with clients to tailor solutions that meet specific needs. Case studies and client testimonials serve as powerful tools to establish credibility and showcase the tangible benefits achieved through this cutting-edge technology.
In conclusion, laser 3D printing is more than just a new technique—it's a transformative force reshaping the capabilities and efficiencies across various industries. As businesses continue to embrace this technology, the potential for innovation seems boundless, driving not only growth but also the evolution of manufacturing and design in the 21st century.