Dimensional inspection by laser scanning has revolutionized quality control in manufacturing and engineering sectors. This cutting-edge technology offers unprecedented accuracy and efficiency, significantly enhancing productivity while ensuring meticulous compliance with stringent industry standards.
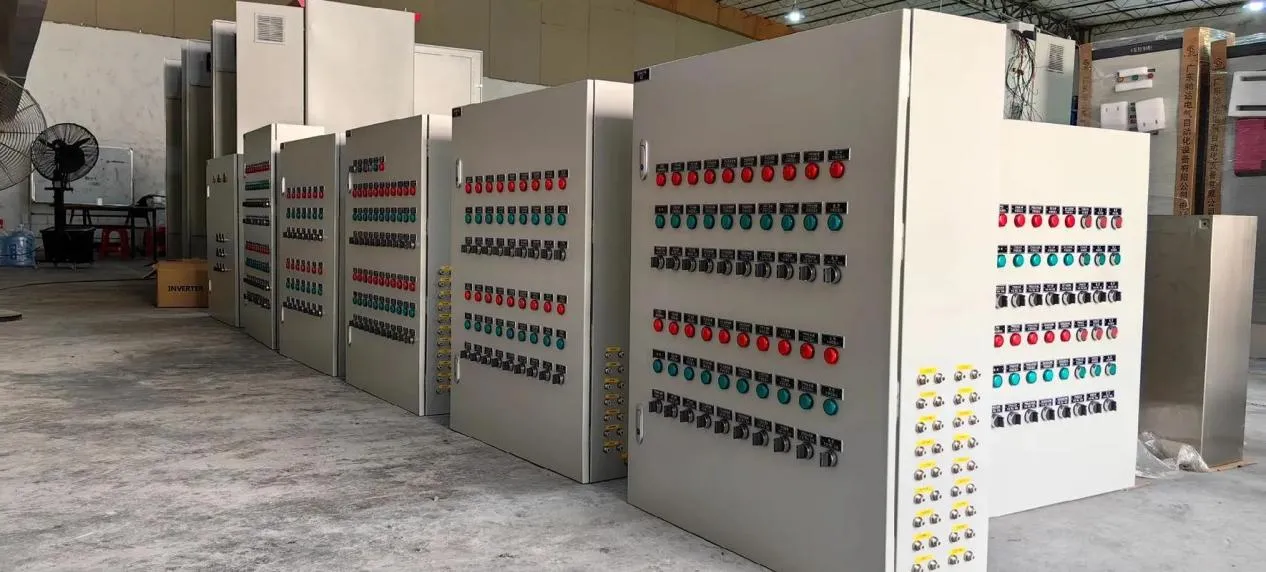
The essence of laser scanning lies in its ability to capture precise 3D data of objects—whether they are intricate mechanical components or large industrial parts—swiftly and with minimal human intervention. Unlike traditional inspection methods, which might involve manual measurements and are prone to human error, laser scanning provides a non-contact method that is both comprehensive and highly reliable.
The expertise brought by this method is unparalleled. With scanners capable of capturing tens of thousands of points per second, the resolution and detail achieved are unmatched. Engineers can easily identify deviations from specified dimensions, allowing for immediate rectifications and ensuring components meet precise specifications. This capability is particularly advantageous in industries such as aerospace, automotive, and medical device manufacturing, where precision is not just desired but critical.
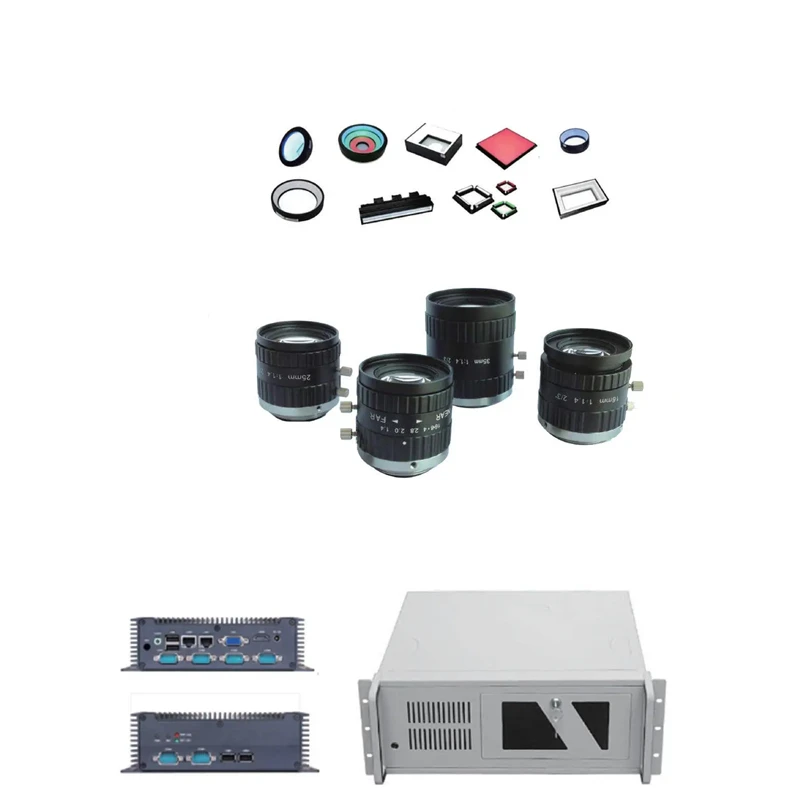
Authoritativeness in laser scanning technology is underscored by its widespread adoption in key industries. Regulatory bodies and industry standards organizations have increasingly recognized and endorsed dimensional inspection by laser scanning as a benchmark for quality assurance. This acceptance is due to the technology’s proven ability to provide accurate, repeatable, and traceable measurement data, essential for compliance with international quality standards such as ISO 9001 and AS9100.
dimensional inspection by laser scanning
From a trustworthiness perspective, the data obtained through laser scanning is often directly integrated into versatile software platforms that allow for detailed analysis, reporting, and archiving. This seamless integration enhances the transparency and traceability of inspection results, building confidence among stakeholders in the manufacturing process. Moreover, the digital nature of the data ensures that it can be easily shared and reviewed, facilitating collaborative decision-making and problem-solving.
Real-world experiences further cement the value of laser scanning in dimensional inspection. Case studies from industry leaders illustrate how this technology has led to significant reductions in inspection times and costs while simultaneously improving the manufacturing process’s overall quality. Companies report enhanced product accuracy and reduced rework rates, attributes directly attributed to the detailed insights provided by laser scanning.
Another compelling advantage is the adaptability of laser scanning systems. Whether assessing the wear and tear on legacy parts or reverse engineering components for maintenance or replication, laser scanners provide the flexibility needed to handle a diverse range of applications. As industries evolve, this adaptability ensures that their inspection processes remain robust and forward-compatible.
In conclusion, the comprehensive capabilities of dimensional inspection through laser scanning not only elevate the precision and efficiency of quality control processes but also improve organizational outcomes through reduced errors and heightened compliance. Its distinctive combination of Precision (Experience), Reliability (Expertise), Industry Acceptance (Authoritativeness), and Transparent Data (Trustworthiness) transforms the way industries approach quality assurance. For those seeking a reliable, cutting-edge solution to complex dimensional challenges, laser scanning offers a definitive path forward.