In the ever-evolving landscape of modern technology, reverse engineering laser scanning has emerged as a transformative tool across multiple industries. Companies seeking to replicate, enhance, or innovate on existing products are increasingly turning to laser scanning for precise, expansive data collection that drives engineering and design processes forward.
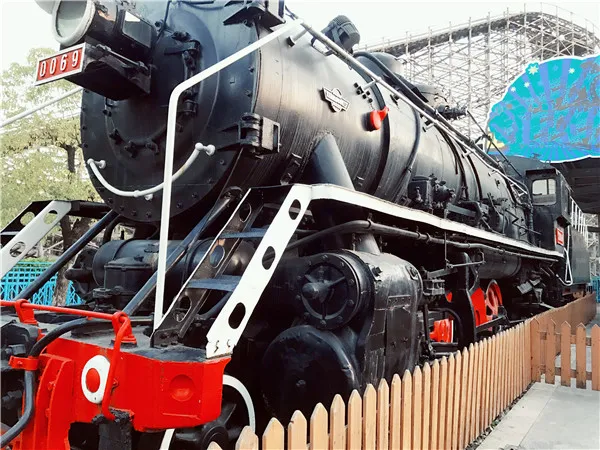
Laser scanning, often categorized under the broader umbrella of 3D scanning, involves the use of lasers to capture an object's exact size and shape, which can then be converted into a 3D digital model. This cutting-edge technology is not only revolutionizing product development but also enhancing quality control, maintenance, and even manufacturing processes by providing engineers and manufacturers with an unprecedented level of detail and accuracy.
The key to mastering reverse engineering laser scanning lies in understanding the profound benefits it offers. At its core, the technique facilitates the creation of highly accurate 3D models reflecting even the finest nuances of the scanned object. This accuracy is paramount in industries such as aerospace, automotive, and healthcare, where precision is non-negotiable. Engineers can seamlessly integrate complex geometrical data into their design workflow, considerably reducing product development timelines and minimizing errors during the manufacturing phase.

Moreover,
reverse engineering through laser scanning empowers companies to improve existing products. By analyzing the minutiae of a competitor's device or a legacy component, the potential for innovation skyrockets. This insight allows engineers to identify design flaws, enhance product performance, and offer refined solutions that meet or exceed market expectations.
Reverse engineering laser scanning
Reverse engineering is not solely about replicating designs; it is also an invaluable tool for quality assurance. Three-dimensional scanning data can be used to conduct thorough inspections and comparisons of physically produced parts against their original design specifications. This ensures that deviations are quickly identified and rectified, significantly reducing the risk of costly defects or recalls.
From an economic perspective, the efficiency and accuracy provided by laser scanning technology can lead to significant cost savings. Designers and manufacturers can reduce resource allocation for modeling and prototyping phases, maximizing the value obtained from every project. The high-resolution data obtained can be rapidly shared across interdisciplinary teams or stakeholders, fostering collaboration and accelerating decision-making processes in product lifecycle management.
To build trust and establish authority within the industry, it is crucial to rely on an experienced team proficient in laser scanning technology. The expertise of skilled professionals ensures that the data captured is both accurate and actionable. Moreover, leveraging the latest hardware and software technologies is imperative to staying at the forefront of advancements in reverse engineering. As laser scanning continues to evolve—with enhancements in speed, accuracy, and accessibility—trustworthy partners adept in handling these tools will lead to superior outcomes.
In conclusion, reverse engineering through laser scanning is a cornerstone technological advancement for creating, scrutinizing, and reimagining products with unprecedented precision and efficiency. By understanding its capabilities and effectively capitalizing on its strengths, companies can enhance their competitive edge, drive innovation, and build products that not only meet but set future industry standards. Choosing the right partner with the right expertise can transform complex challenges into growth opportunities, fostering trust and reliability in this rapidly advancing field.