Building a 3D laser scanner a comprehensive guide
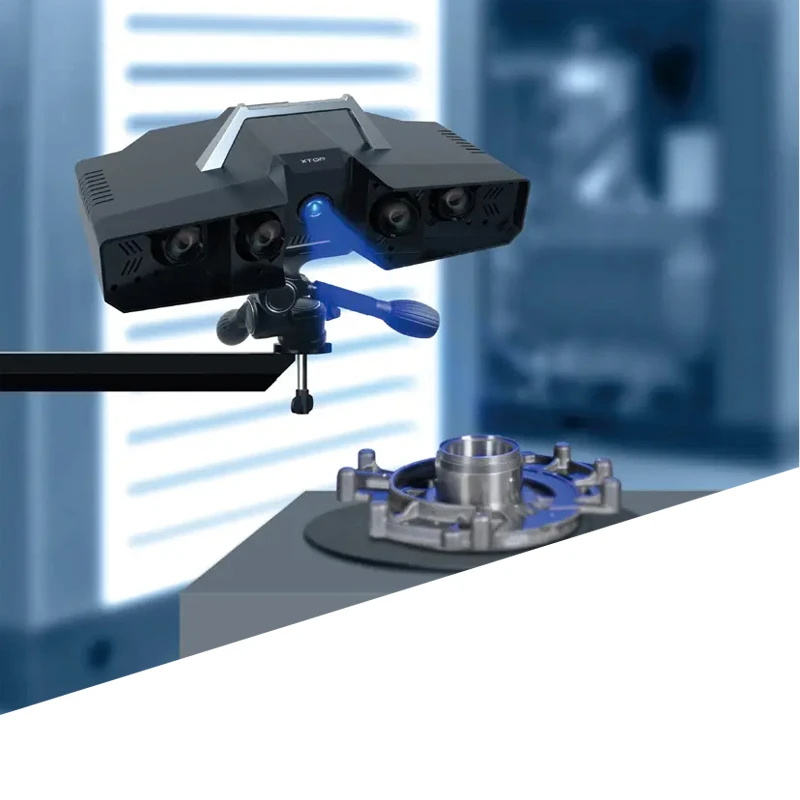
Creating a 3D laser scanner from scratch is an intricate process that combines technical expertise, precision engineering, and a comprehensive understanding of optics and computer algorithms. For anyone venturing into this realm, it's essential to leverage one's knowledge in physics, computer science, and electrical engineering. This process not only fosters a deeper understanding of how 3D scanning technology works but also allows one to tailor the scanner to specific needs, potentially enhancing its performance and accuracy beyond commercially available models.
The first step in constructing a 3D laser scanner involves selecting the appropriate laser and sensor components. The laser, usually a laser diode, is the system's core, emitting a coherent beam of light that will be used to illuminate the object's surface. The choice of laser depends on the application's requirements; for precision scanning, a red or green laser is often preferred due to its visibility and the ease of filtering out external light interference.
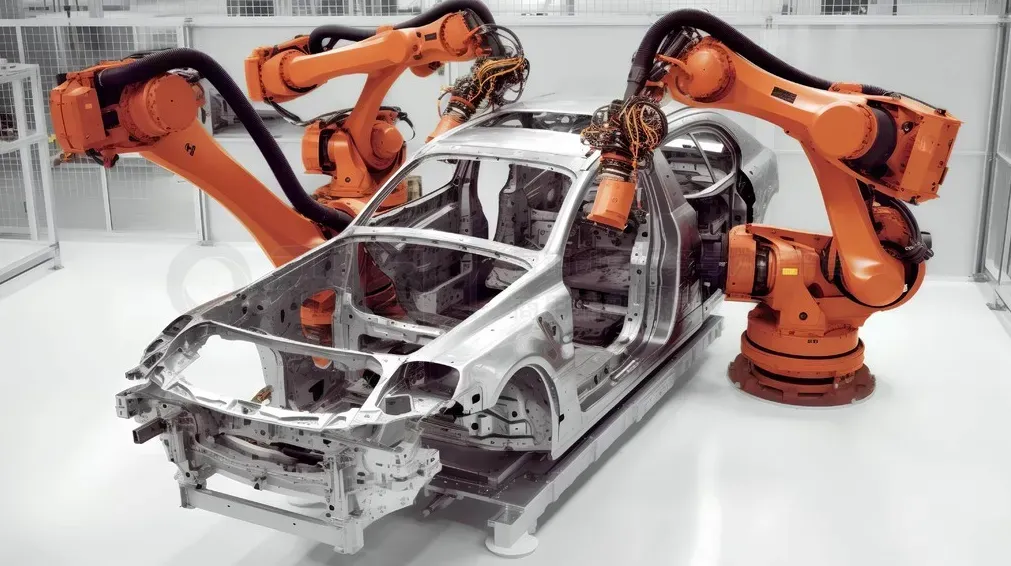
Simultaneously, selecting an appropriate sensor is critical. CMOS and CCD sensors are commonly used due to their high sensitivity and resolution. The sensor's role is to capture the variations in light intensity as the laser projects across the object, essentially collecting thousands of data points that represent the surface's contours. For high-resolution scans, a high-megapixel sensor ensures finer detail but requires a powerful processor to handle the data.
Aligning the laser and sensor is a crucial step in ensuring the accuracy of the 3D scanner. Calibration involves precisely controlling the angle and distance between the laser and the sensor, often requiring custom mounts or precision tripods. The laser beam should strike perpendicularly to the object surface to minimize distortion and ensure higher fidelity in capturing surface features.
Next, integrating motion control systems to manipulate the object or the scanning apparatus itself ensures comprehensive coverage of all object surfaces. This can involve the use of motors to rotate the object or move the scanner along designated paths. The complexity of the mechanism will depend on the size and intricacy of the objects being scanned.
3D laser scanner construction
The backbone of a successful 3D laser scanner is its software. Writing custom software can be challenging yet rewarding. The program must analyze the captured data, translating light patterns into digital signals representing the object's surface. This involves algorithms that calculate distance based on the time of flight of the laser light or triangulation methods for determining spatial coordinates.
Ensuring the software can process the data efficiently is paramount, as 3D scanning generates substantial data. Implementing parallel processing and leveraging the computational power of modern GPUs can optimize performance, enabling real-time processing for applications requiring immediate analysis, such as quality control in manufacturing.
One must also incorporate error-correction algorithms. Real-world surfaces are rarely perfect, and variations can introduce significant noise into the data. Techniques such as median filtering or using machine learning models trained on large datasets of scanned objects can clean the data, enhancing accuracy and reliability.
Safety is another paramount consideration when constructing a 3D laser scanner. Lasers, especially those of higher power, can be hazardous. Safety protocols, including protective eyewear and warning systems, must be in place to prevent accidental exposure. Incorporating safety interlocks and using laser enclosures can safeguard users, especially if the system is intended for environments where untrained personnel might be present.
The final step involves extensive testing and refinement. Scanning a variety of objects helps identify any systematic errors in the apparatus. Testing should cover various materials and surface textures, as different reflectivity and transparency levels can affect scanning results. Iterating upon the design, recalibrating both hardware and software components as necessary, ensures robustness and versatility.
Building a 3D laser scanner from scratch not only advances one's technical prowess but can also enhance a professional's credibility and authority within the fields of engineering and design technology. By mastering the construction and implementation of such complex devices, individuals position themselves at the forefront of innovation, contributing valuable insights to the ever-evolving landscape of 3D scanning technology.