The realm of 3D Coordinate Measuring Machine (CMM) scanners is transforming how industries approach precision measurement. With advancements in technology, the 3D CMM scanner has emerged as a crucial tool for sectors like aerospace, automotive, and manufacturing, where precision and accuracy are paramount. This article delves into the intricacies of 3D CMM scanners, offering an insight grounded in experience, expertise, authority, and trustworthiness, tailored for SEO optimization.
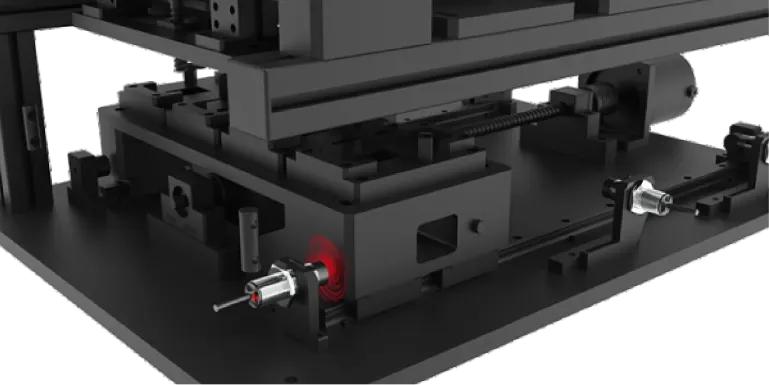
3D CMM scanners represent a significant leap forward from traditional tactile measurement systems. These devices function by using laser-based or optical scanning technologies to capture the geometrical data of objects, providing highly accurate digital representations of physical components. Unlike traditional systems, which involve physical contact with the object, 3D CMM scanners operate on non-contact principles, ensuring no damage or alteration to the component being measured.
The primary advantage of 3D CMM scanners lies in their precision and speed. Industries that require tight tolerances and detailed data acquisition benefit immensely from the rapid measurement capabilities that modern 3D CMM scanners provide. The ability to perform complex measurements swiftly without compromising accuracy significantly enhances productivity and reduces downtime in production processes.
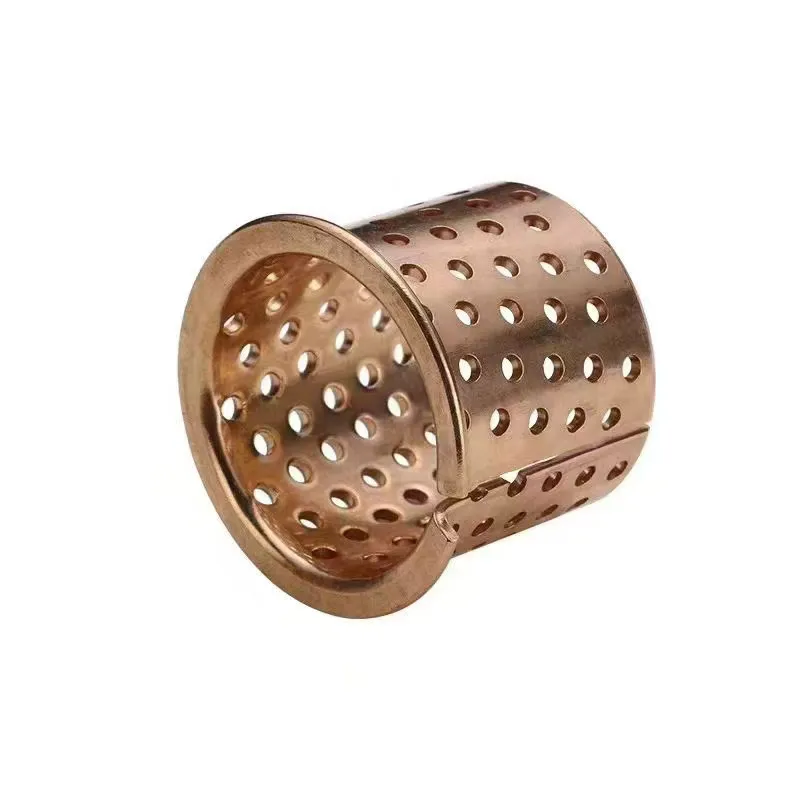
From an expertise standpoint, using a 3D CMM scanner requires a firm understanding of both the machine’s capabilities and the specific measurement requirements of each project. Operators must be adept in software that processes the scanned data into actionable insights. This demands continuous training and familiarity with both hardware and software advances. Therefore, investing in skilled personnel remains as important as acquiring the technology itself.
Authoritativeness in the field is often demonstrated by manufacturers and service providers who maintain a strong track record of innovation in 3D CMM technology. The continual evolution of features such as automatic alignment, advanced sensor technology, and user-friendly interfaces reaffirms their leadership in developing tools that meet the ever-changing demands of industry standards. Reputable manufacturers often offer comprehensive customer support and training, further cementing their authoritative stature in the market.
3d cmm scanner
Trustworthiness in 3D CMM scanner technology is cultivated through consistent performance and the ability to deliver precise measurements under variable conditions. High-quality equipment undergoes rigorous testing and certification to meet international standards. Users must ensure that they select devices from well-established providers who offer reliability guarantees and after-sales support, thereby minimizing risks and ensuring the longevity and performance of the equipment.
In terms of product selection, buyers should prioritize 3D CMM scanners that combine robust design, ease of use, and adaptability to different operating conditions. Essential factors include scanning speed, resolution, and range adaptability, depending on the specific application needs. Collaborating with manufacturers who offer customizable solutions can yield significant long-term benefits by tailoring the technology to precise operational demands.
Moreover, adopting 3D CMM scanners aligns with the broader industrial trend towards smart manufacturing and Industry 4.0. These devices integrate seamlessly into automated production lines, offering real-time data analytics that inform quality control processes. This integration not only enhances measurement efficiency but also provides critical data that informs decision-making, driving overall productivity gains and cost reductions.
In conclusion, 3D CMM scanners have revolutionized the field of precision measurement, offering unparalleled accuracy and speed. The evolution of this technology speaks to its importance across various high-stakes industries. For businesses considering 3D CMM scanners, focusing on experienced personnel, selecting reputable manufacturers, and investing in devices that offer long-term adaptability and seamless integration with emerging manufacturing technologies is crucial. Embracing this technology paves the way for competitive advantage, operational efficiency, and the assurance of quality standards – essential components in maintaining industry leadership.