In the realm of industrial automation and quality control, the 3D profile sensor stands as a pivotal technology transforming how businesses conduct inspections, monitor production processes, and ensure quality. These sensors provide invaluable three-dimensional data, enhancing precision and reliability across various applications. As the global market evolves, understanding the key benefits and capabilities of 3D profile sensors becomes crucial for any business aiming to leverage technological advancements for competitive advantage.
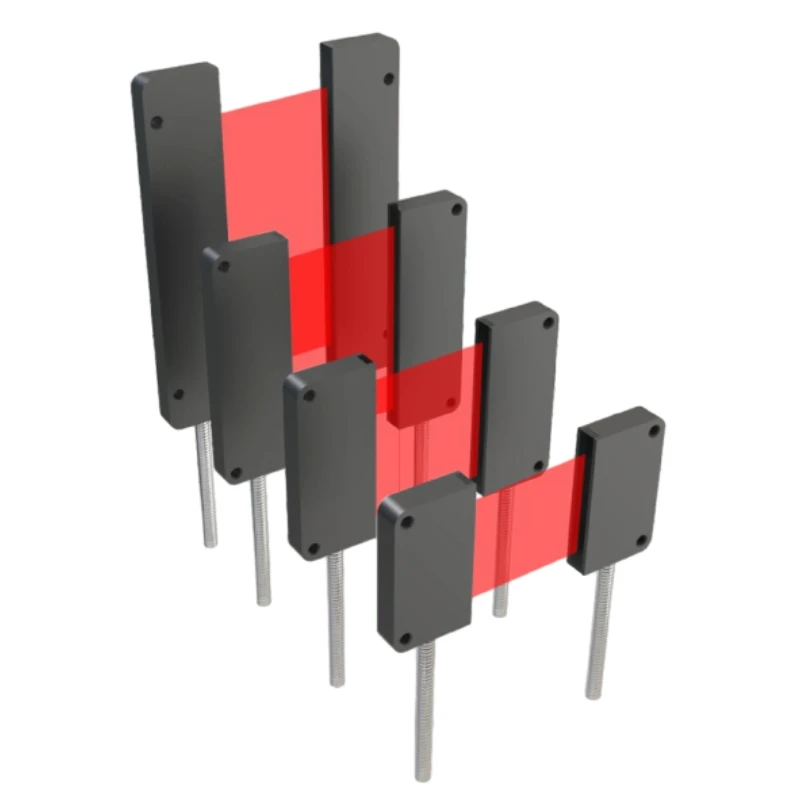
3D profile sensors employ advanced optical technology to capture detailed information about the shape and dimensions of objects. By projecting a laser line over an object and capturing the reflected light with a camera, they generate precise 3D profiles. The collected data helps in object measurement, quality inspection, and even real-time decision-making on production lines. For businesses in manufacturing, automotive, electronics, and other sectors where precision is paramount, these sensors offer unparalleled benefits.
A standout feature of 3D profile sensors is their ability to perform non-contact measurements, which safeguards delicate or hazardous materials and enhances workplace safety. This approach prevents wear and tear on components, reduces maintenance requirements, and promotes a safer working environment by eliminating the need for manual handling during inspections. Furthermore, non-contact measurements enable rapid data capture without interrupting ongoing processes, thereby increasing operational efficiency.
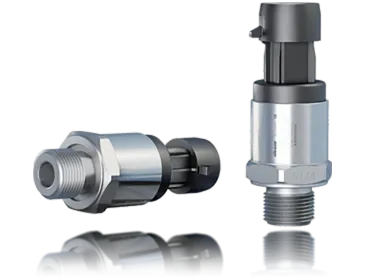
In terms of accuracy, 3D profile sensors outperform traditional methods with high-resolution imaging and measurement capabilities. They can detect minute deviations from specifications, facilitating early intervention and reducing waste. The precision offered by these sensors ensures that products meet stringent industry standards consistently, significantly boosting a company's reputation for quality.
3D contour sensor
Moreover, the integration of 3D profile sensors into smart manufacturing systems aligns with the broader Industry 4.
0 trend. These sensors can seamlessly communicate with other machines, feeding real-time data into centralized systems for analysis. Such integration enables predictive maintenance, process optimization, and enhanced supply chain visibility. Consequently, businesses can achieve not only cost savings but also improve their sustainability by minimizing resource consumption and waste.
The adoption of 3D profile sensors also facilitates customization, as they allow for quick adaptations to new product designs or changes in customer specifications. They enable manufacturers to produce small batches without compromising on quality or incurring high costs. This flexibility is critical in today's market where consumer demand for personalization is on the rise.
To effectively implement 3D profile sensors, businesses should consider partnering with reputable suppliers that offer robust technical support and customization options. Selecting the right sensor for a specific application involves understanding various factors such as measurement range, resolution, and environmental conditions. Expert consultation can ensure that the chosen technology aligns perfectly with operational needs and long-term strategic goals.
In conclusion, integrating 3D profile sensors into industrial processes presents a strategic advantage for businesses looking to enhance precision, efficiency, and overall product quality. With their ability to provide detailed and reliable data, these sensors play a vital role in advancing manufacturing capabilities, reinforcing the importance of expertise and innovation in the rapidly evolving industrial landscape. As companies continue to navigate the complexities of modern production, embracing cutting-edge technologies like 3D profile sensors will be essential for sustained success and market leadership.